Building houses in factories for the Commonwealth Games was meant to help the housing crisis. What now?
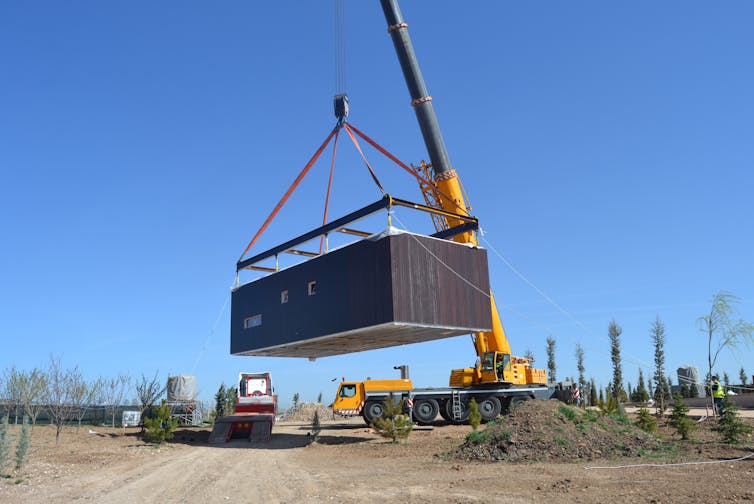
Huge sporting events come with substantial public investment in housing. After Melbourne hosted the 1956 Olympics, about 600 houses in the athlete village became public housing in West Heidelberg. After Melbourne hosted the 2006 Commonwealth Games, the athlete village in Parkville was largely sold off, with 320 houses going to social housing.
Victoria’s now cancelled 2026 Commonwealth Games were meant to have the same effect in the state’s smaller cities. New dwellings were intended to help boost social and private housing supply amid the ongoing housing crisis. Ironically, the broader housing crisis may have contributed to the cancellation, as worker shortages and building material price spikes took their toll.
Importantly, half of these were to be prefabricated and modular buildings. This would speed up construction and demonstrate what’s now possible. While regions like Scotland now do almost all of their construction in factories, Australia is only just beginning.
So is cancellation of the games a blow for prefab construction in Australia? It’s a PR setback, given the attention it would have received. The state government has committed to building 1,300 new homes in the regions, the same number intended for the games. As yet, we don’t know if these will be prefab.
Building the prefab profile
Victoria agreed to host the games only last year. That gave very little lead time – the games will start in just two and a half years, assuming a new host is found. This rapid time frame was why Victoria’s government looked to prefab to provide the thousands of dwellings needed for officials, athletes and workers.
After the games, these houses in Victoria’s fast-growing host cities of Bendigo, Ballarat, Geelong and Shepparton were meant to boost social and affordable housing supply.
The plans were a welcome shot in the arm for Australia’s prefab industry, which was just 5% of new builds this year, though it’s expected to reach 10% by 2030. Scaling up the use of prefabrication will need government support and leadership.
Leading prefab jurisdictions like Scotland and Sweden have needed government support to get to where they are, with prefab accounting for 84%.
Why look to prefab homes at all?
Factories are a way of producing standardised products more cheaply. Bringing these techniques to bear on houses cuts costs, slashes waste by up to half, and can quickly boost housing supply. Waste can be cut by precise standardised measurements and the use of low-carbon materials like timber or hybrid steel-timber reduces environmental impact.
You might think prefab homes would all look the same or lack quality. But standardisation can often be high quality. When construction is done in a factory setting with a controlled environment, it can be easier to ensure it’s airtight, well insulated and meets standards.
Prefab factories can reduce the impact of weather on construction, though it does create another challenge – transporting the dwelling to the site.
It’s not just for single or double-storey buildings. More than 500 apartments were delivered to a vacant site in London using modular systems, which were then slotted into place to build Ten Degrees, the world’s tallest residential modular building to this date. The process cut embodied carbon by up to 40%, according to the building’s designers.
Boosting prefab without the games
In a recent report led by Master Builders Victoria, we examined how experiences of the Birmingham 2022 and Glasgow 2014 Commonwealth Games in the UK helped the construction industry innovate in areas like prefab housing.
Preparations for the Birmingham games faced the unprecedented challenge of the COVID pandemic. As a result, the planned athlete village was never used for athletes, and the units built eventually became private and social housing. Prefab techniques were used to build 430 apartments.
Even with the COVID challenge, these apartments were completed ahead of time. In contrast to traditional construction methods, there was more use of the local workforce.
Why isn’t Australia embracing these techniques?
Inertia. To make prefab housing mainstream in Australia will mean major changes to the way things are done at present. Our construction industry is not always able to take risks, which makes innovation challenging.
One way to get around this is to create the demand for these types of houses. In Victoria, the government’s pledge to still deliver the promised regional housing could be tied to prefabrication, to help deliver high quality, sustainable and affordable housing more quickly and begin reshaping the wider industry.
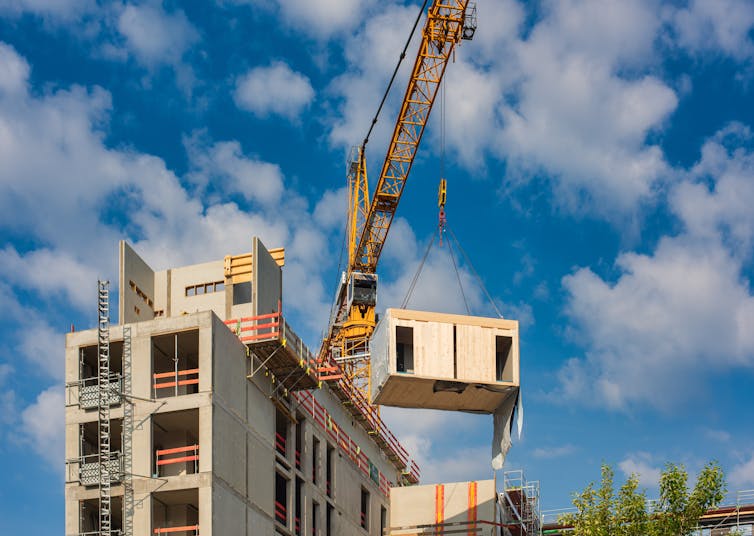
Even with the games gone, other pressures like the rental and housing crisis are only intensifying. Prefab could help here by offering more affordable and sustainable housing as an option, especially outside metropolitan areas where the cost of land makes up a smaller proportion of the cost of a house or as urban infill.
The games would have helped supercharge the prefab industry. But Australia has an urgent need for more housing. Prefab could help deliver this more cheaply and more sustainably.
Former RMIT researcher and Master Builders Victoria adviser Joana Correia contributed to this piece.
Louise Dorignon, Vice-Chancellor Postdoctoral Research Fellow, RMIT University and Trivess Moore, Senior Lecturer, School of Property, Construction and Project Management, RMIT University
This article is republished from The Conversation under a Creative Commons license. Read the original article.
Comments